New England is a hub for high-performance builders who foster a culture of ongoing innovation, pushing the envelope on energy efficiency, sustainability, and durability in their building practices. BPC Green Builders, a construction firm based out of Ridgefield, CT, fits this bill. Their team is no stranger to building science and airtight construction. So why in the world would a single-family builder like this incorporate AeroBarrier in their air sealing strategy?
Meeting or exceeding airtightness targets is more important now than ever before. Designers like Trillium Architects are utilizing energy modeling software during their development process to determine sizing of mechanical systems, heating and cooling loads, and renewable energy integration to optimize building performance and occupant comfort. If a building fails to meet their air leakage requirement, many of the systems specified during the design phase will be insufficient, potentially resulting in increased energy costs, compromised indoor air quality, and a greater risk of moisture-related issues. Ultimately, a leaky building envelope can trigger a cascading series of unfortunate events throughout a building’s life cycle.
BPC Green Builders had a mandate to meet or exceed 1 Air Change per Hour on this 4,900 square foot home in Westport, CT. Like many quality builders, they performed some diagnostic blower door testing post rough-in to ensure that their weather and airtight shell would hit this target before insulating and sheet rocking. When the results came in at 2 ACH50, their team knew that they had to identify any large bypasses and leaky assemblies/components within the building envelope.
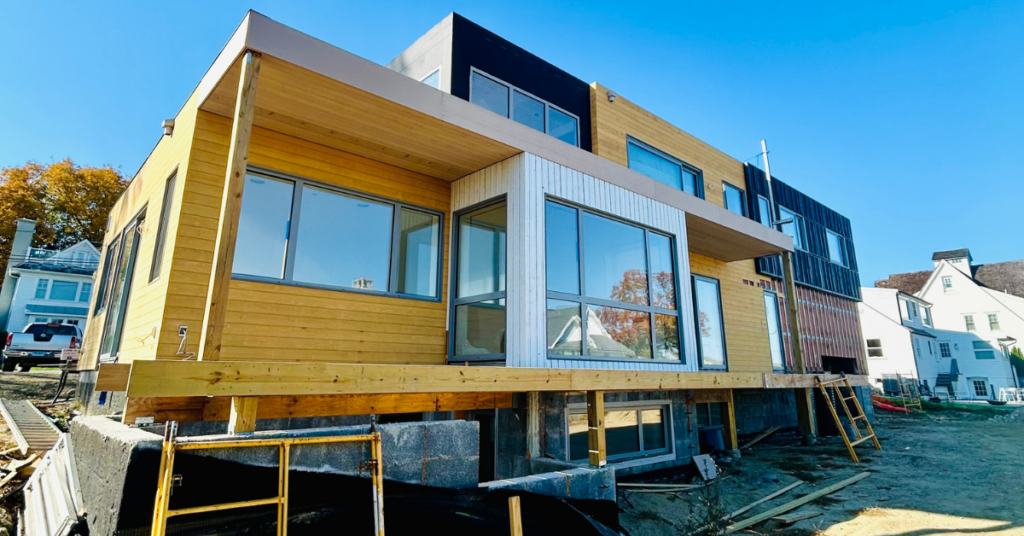
The diagnostics demonstrated that The Perfect Block ICCF Foundation System, a green building product that minimizes the use of concrete, was air permeable. In addition to the porous foundation, the window and door units throughout the home were surprisingly leaky through the glazing and joints/miters in the frames. Even though their detailing of the continuous air control layer was completely dialed in, the challenges posed by these two leaky building components required the BPC Team to seek alternative air sealing strategies.
The air leaks in the Perfect Block were compiled of thousands of microscopic holes, and with framing, mechanicals, plumbing, and electrical obstructing access to the foundation, coating this surface with some sort of liquid flashing or a membrane was not feasible. In addition to this, The Perfect Block foundation system is not necessarily compatible with these types of building products.
The windows and doors also posed a unique challenge. Did the CFM of air infiltration through the windows and doors exceed the manufacturer’s allowable amount of air leakage, or was the grade of these units not up to par for a building with an aggressive air sealing requirement? Not only is this a complicated question that is difficult to answer, but it’s an issue that cannot be remedied through supplemental manual air sealing measures.
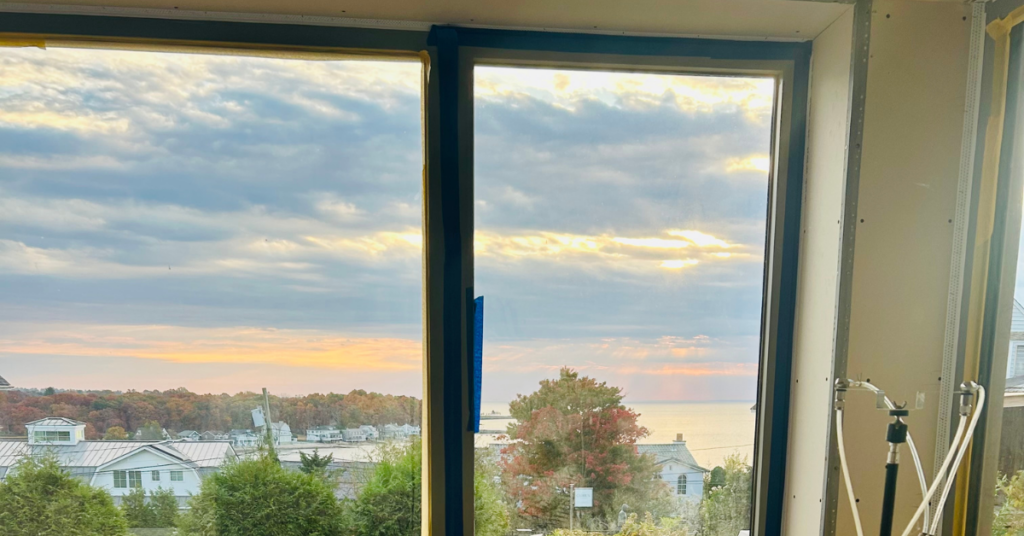
We could spend all day hashing out the problems at hand, which is fun for building performance geeks like me, but were there any viable, cost-effective solutions that minimized or even eliminated any potential rework? Our air sealing process which utilizes Aeroseal’s breakthrough technologies was the ideal solution to mitigate air infiltration through the Perfect Block Foundation System, and ensure the full building met or exceeded the air sealing target. Furthermore, our masking process and blower door testing capabilities were able to provide BPC Green Builders with a definitive answer regarding the window and door allowable levels of air leakage.
Let’s start with the phase one, post rough-in AeroBarrier Application in the cellar. BPC Green Builders isolated the basement from the rest of the house using plywood and tape at the top of the interior stairwell, ensuring that we would be able to pressurize and seal the basement independent of the top two floors. This strategy allowed the AeroBarrier sealant to be pushed directly to all of the pin hole leaks in the foundation system.
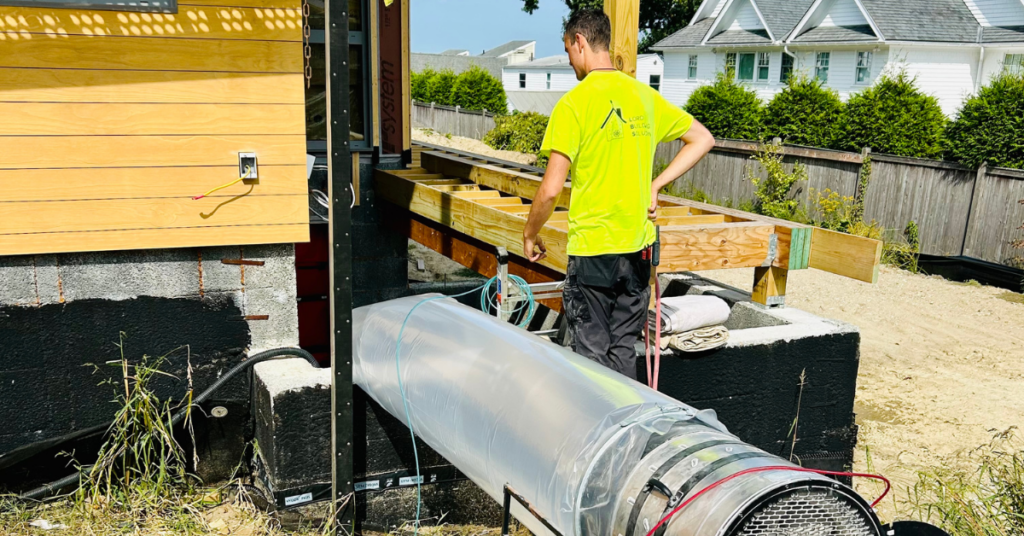
One of the distinct aspects of the AeroBarrier process is that it can seal holes as small as a human hair, and you don’t need to know where the leaks are in the first place. Our physics-based process is automated and removes the need to identify the air leaks and seal them manually. The phase one AeroBarrier Application resulted in a reduction of 0.6 ACH50, all of which was present in the Perfect Block Foundation system.
Since there was still 0.4 ACH50 to address and lingering questions about the windows and doors, we returned to the jobsite one month later after the drywall was hung for the phase two AeroBarrier application on the whole house. Our team was able to reduce the remaining air leakage in the entire building by 57.3%, equivalent to a 46.3 square inch hole. These results gave us confidence that we were going to meet or exceed the 1 ACH50 requirement, but two critical steps remained.
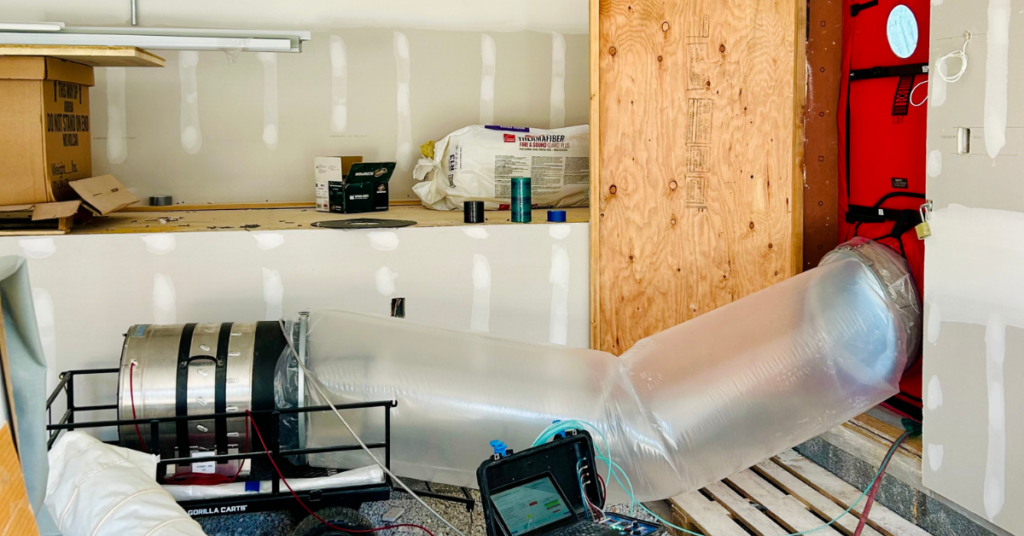
With all the operable components and joints in the window and door frames masked off, we pressurized the home to 50 pascals and began to take our readings. We removed the tape from each window and door, one at a time, paying close attention to the increase in CFM for each unit. This allowed us to determine how much air infiltration existed in each type of window and door, as well as the total accumulation of leakage in these units which equaled approximately 200 CFM!
After all masking was removed, we flipped the fan around and performed the final depressurized blower door test to verify that the full building exceeded the 1 Air Change per Hour target. With so much at stake, my palms were sweaty, knees weak, and arms heavy, I took a deep breath and viewed the report. Our multi-point blower door test results came in at 0.74 ACH50. Our two-part mission to Westport, Connecticut was accomplished, with the foundation system sealed, the overall airtightness requirement met, and the glazing data provided to the BPC Green Builders Team.
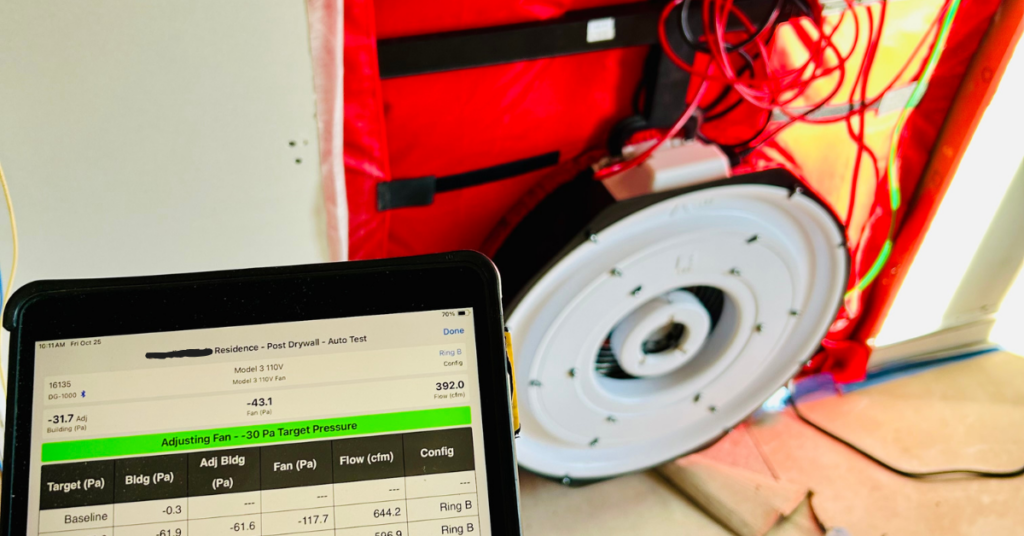
So often builders, developers, and architects are faced with similar challenges that were present during this high-performance build. Whether the air leakage challenges are due to incorporating innovative or inadequate building products, budget constraints, design hurdles, or quality control, LBS can be one piece in your construction puzzle.
Trust me, we enjoy demonstrating the mind-blowing capabilities of AeroBarrier in very leaky structures. Some of our applications have resulted in more than a 20 Air Change per Hour reduction in 180 minutes of seal time. This two-part seal may not have been the most impressive by the numbers, but it was incredibly rewarding and proves that there is a value proposition for AeroBarrier in New England’s high-performance building hub.
Builder: BPC Green Builders
Designer: Trillium Architects
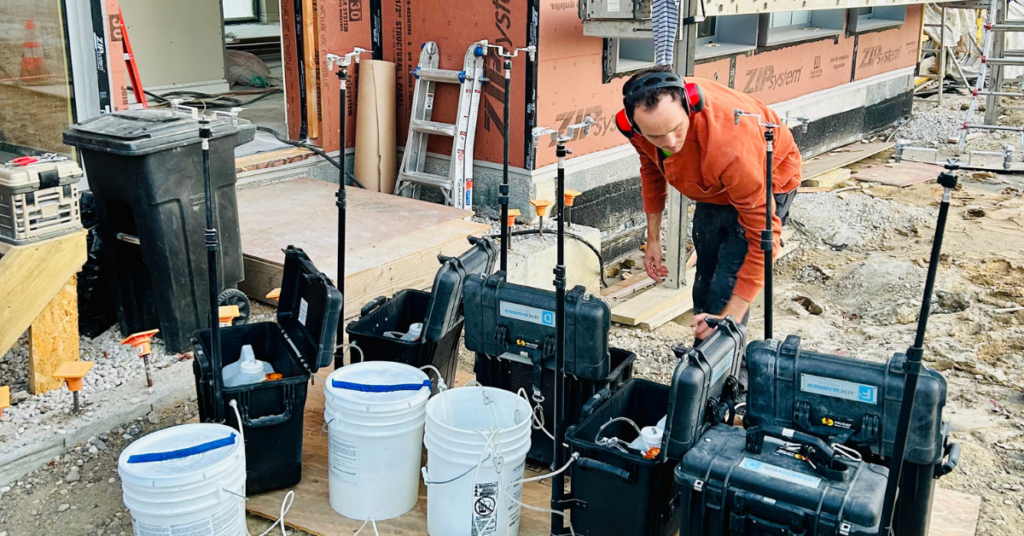